What is Spin Coating & How Does it Work?
Spin coating is one of the industry-leading methods of depositing a thin film of material onto a functional substrate. There are no chemical constraints placed on thin films; they are simply any layer of material ranging from just a few micrometers (μm) in thickness down to a single nanometre (nm). Consequently, they are of interest to an enormous cross-section of end-users and market sectors.
Background to Thin Films
Thin films are routinely used as electronic, optical, protective, even decorative coatings. In fact, engineers trace the origins of thin-film deposition back to decorative gold leaf coatings on ornaments dated as early as 2600 BCE. The method of depositing extremely thin gold coatings is known as gilding; a term that encompasses even the most rudimentary technique where gold foil was simply hammered onto a surface with an intermediary adhesive layer. Although this may sound crude by today’s standards – where thin films can be chemically synthesized in ultra-high vacuum (UHV) conditions – some of the most common methods of thin film deposition still rely on the application of force to coat a substrate: Spin coating, for instance.
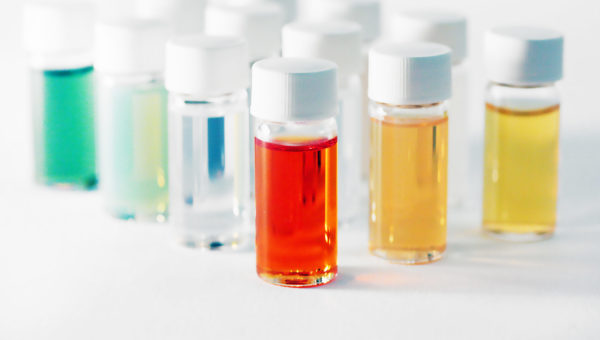
What is Spin Coating?
Spin coating is a method of producing uniform thin films using centrifugal force as the method of deposition. In a typical process, a uniformly planar substrate (i.e. an electronic wafer) is secured on a spindle and a liquid precursor/nanoparticle solution is dispensed via a syringe onto the center of the workpiece. This substrate is then centripetally accelerated which causes the liquid to spread across the surface via centrifugal force. Excess material is thrown off the edge of the rotating substrate, leaving a uniform thin film on the surface.
How Does Spin Coating Work?
This process works by carefully controlling the speed relative to various material properties of the solution. Viscosity is prime among these properties as it determines the resistance to uniform flow, which is vital in achieving a uniform surface finish. Spin coating is subsequently carried out across an extremely wide speed range, from as little as 500 revolutions per minute (rpm) to as much as 12,000 rpm – depending on the viscosity of the solution.
Viscosity is not the only material property of interest in spin coating, however. Surface tension may also affect the flow characteristics of the solution, while percent solids can impact the required thin film thickness to achieve specific end-use properties (i.e. electrical mobility). Spin coating is subsequently conducted with a full understanding of the relevant material properties, with plenty of adjustable parameters to suit distinct characteristics (flow, viscosity, wettability, etc.).
Spin coating can be carried out using either a static or dynamic start, each of which can be programmed for user-defined acceleration ramping and various spin speeds. It is also important to allow for fume exhaust periods and drying times as poor venting can result in optical flaws and non-uniformities. For example: Swirl patterns may indicate that the exhaust rate is too high for a solution that takes longer to dry. There is no one-size-fits-all solution when it comes to spin coating, and each process must be carried out with a holistic approach to the substrate and coating solution in question.
Spin Coating Materials from Avantama
Avantama is one of the world’s leading suppliers of nanoparticle solutions and custom formulations for electronics applications. With a robust catalog of off-the-shelf formulations suitable for spin coating and an unmatched custom synthesis program, we are confident that we can develop the materials you need for a reliable, high-performance spin coating process.
If you would like any more information about spin coating with Avantama products, simply contact a member of the team directly.