How are OLEDs Made?
Organic light emitting diodes (OLEDs) are photo-emissive panels widely used in the formation of ultra-thin digital displays. They represent some of the highest quality TVs, computers, and handheld digital devices ever made, with exceptionally low levels of power consumption and ultra-high definition capabilities. OLEDs directly compete with conventional liquid crystal displays (LCDs), and are widely considered the new benchmark for image quality – but this innovative material is finding wider application in a surprising range of markets.
The possibilities enabled by the formation of transparent and flexible OLEDs has opened realms of possibility, from embedded displays in window glass to wearable computers. OLED products, therefore, have potentially limitless applications beyond the display market, with countless opportunities to radically alter our daily lives – but how are these innovative materials made?
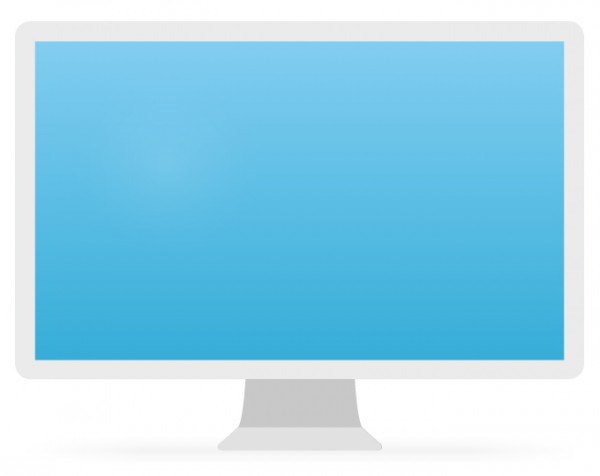
Manufacturing OLED Arrays
Anodes are applied to a substrate material of plastic or glass. Organic, conductive molecules dispersed throughout a solvent are then applied to the anode, commonly through inkjet processing.
Inkjet processing is a relatively cheap and repeatable manufacturing method which is used for a range of printing methods, from photographs to printed circuitry. In the case of OLEDs, inkjets spray the substrate material with a specialty dispersion, coating it with a uniform layer of conductive molecules. A second layer is then added to the matrix through similar processes, this one comprised of emissive molecules – and further layers can be applied if necessary.
These organic layers are finished with the application of a cathode, effectively sandwiching the organic layers in a self-contained circuit, before a final seal of glass or plastic is applied to complete the OLED display.
When an electrical charge is applied to the array, it results in a flow of electricity from the cathode to the anode. The anode draws electrons from the conductive layer while the emissive layer receives electrons from the cathode, causing a flow of displaced electrons which results in electrofluorescence. This process makes conventional light-emitting diode (LED) backlights redundant, vastly improving energy efficiency and allowing for the formation of increasingly thin, flexible, and transparent OLEDs.
Innovative OLED Products
The first OLED TVs that were made commercially available showcased the inherent flexibility of the technology with striking curved designs. They were reportedly manufactured this way to improve the viewing experience, but the design also made a definitive statement about what this next-generation technology could do.
Emerging prototype OLED displays have already taken the innovative nature of the technology a step further, with the unveiling of UHDTVs that can be safely rolled-up when not in use. Researchers and developers have reiterated the desire to integrate OLEDs into car windows and windscreens for unobtrusive displays that would vehicular interior design.
Just as crucially, the expensive manufacture of OLEDs is gradually reducing, with the application of cheaper, safer, and more readily available specialty dispersions for application through traditional printing methods.
OLED Products from Avantama
Avantama is a leading developer of specialty solutions for a range of markets, including the formation of specialty dispersions for OLED processing. Our products are available to a range of different work functions and specifications, and can attain full performance levels at annealing temperatures as low as 100°C.
If you would like any more information about Avantama’s solutions for OLED manufacture, please do not hesitate to contact us.